In 1968, as workers hoisted steel beams more than 1,100 feet above Chicago’s lakeshore, the John Hancock Center (now 875 N Michigan Avenue) reached its full height. The achievement would forever change not only Chicago’s skyline, but the entire field of tall building design and engineering. Hancock’s “braced tube” structural system—devised by SOM engineer Fazlur Khan and architect Bruce Graham—introduced a new era of efficient skyscraper design, and now, more than 50 years later, SOM designers continue to improve the concept.
The origin of Hancock’s iconic structural system can be traced to an earlier Chicago project led by the same design and engineering team: the Dewitt-Chestnut apartment building. For this 42-story tower, Khan devised a structural perimeter of closely spaced concrete columns, which together perform like a thin-walled tube cantilevering from the ground. Dubbed the “framed tube,” this system of perimeter columns was strong enough to absorb strong wind forces, allowing for fewer interior columns spaced further apart. The result: an efficient structure with highly flexible interior spaces.
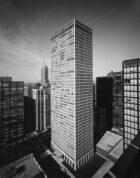
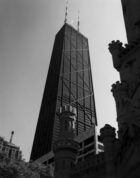
For John Hancock Center, Khan envisioned an even more efficient structural system by replacing the framed tube, as used at Dewitt-Chestnut, with a diagonal steel braced truss on the building’s perimeter, reducing the structural material needed for a tower of this height. The Hancock marked a breakthrough in tall building efficiency—with more improvements to come.
SOM’s research team: In pursuit of efficiency
Starting around 2008—approximately 40 years after the construction of the John Hancock Center—SOM partner and structural engineer William F. Baker led a research team to explore optimal truss geometries. One finding was that the Hancock’s X-brace configuration could be improved by moving the central intersection node upwards at the three-quarters height of the braced bay, increasing material efficiency by about 10 percent. (It is interesting to consider that the iconic X-brace geometry of the John Hancock Center would likely have a different design, if the team had had this knowledge at the time.)
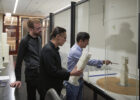