A research team at the University of Colorado Boulder believes that a new generation of biological materials could turn the construction industry into a force to heal the planet. The products they are developing — including algae-based concrete — are the types of solutions that architects at SOM are seeking in order to create zero-carbon and carbon-negative buildings. With these goals in common, Dr. Wil V. Srubar, director of the Living Materials Laboratory, and Yasemin Kologlu, design principal at SOM, have become close collaborators. Here they share their big ideas on how biomaterials could spark a revolution in the building industry. This is the first interview in a series focused on strategies to decarbonize the built environment.
Wil and Yasemin, how did you connect?
Wil Srubar: In early 2020, my lab group, together with other colleagues at the University of Colorado Boulder, published our first study on engineered living building materials. We got a lot of press coverage — a New York Times article, an interview on NPR. I was pleasantly surprised to get an email from Yasemin and others at SOM who wanted to know more about our work.
Yasemin Kologlu: I didn’t even know about the New York Times or NPR articles, to be honest! I was leading a research initiative at SOM focused on finding solutions to reach zero carbon across all of our projects, and even push beyond. We wanted to look outside of the building industry for ideas — to academia, research institutes, manufacturers, and thinkers. We narrowed down different systems and methods that we could use, and Wil’s work on biological materials was among those.
Why are building materials such an important focus right now?
Yasemin: We have a responsibility to address climate change, as designers and design professionals. We all know by now that 40 percent of global carbon equivalent emissions come from the building industry and from buildings themselves.
In our work we always try to reduce energy demand, energy use, operational carbon, operational energy, and another big piece of the puzzle is embodied carbon — both for up-front and end-of-life carbon. When we look at the whole life-cycle of a building, we cannot ignore the carbon emissions of materials in this equation. And when we consider the impact across the entire industry, we simply cannot continue building the way we’ve been used to. It’s about time for us to look at alternatives, new ways of thinking, new materials that help us change the norm.
Wil, you’ve been developing some of these alternatives. Tell us about your work and what you envision building materials could be in the future.
Wil: It was influential for me to learn that more than 11 percent of global CO2 emissions are attributed directly to construction material manufacturing. As structural engineers, that’s our responsibility, that 11 percent.
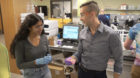
In my research group, the Living Materials Lab, we believe that biology has figured out a lot of things for us — we just need to pay closer attention. We started to look at how we can produce materials for buildings by leveraging two mechanisms that nature uses to store and sequester CO2 in material form. One of these is photosynthesis. We all learned this in third-grade biology — that every plant, seed, tree, even algae, as it grows and replicates, sucks up CO2 from the atmosphere and stores it in the sugars, proteins, and carbohydrates of those organisms. That is physical materiality produced by drawing down CO2 from the atmosphere.
The second mechanism is carbonate mineralization, a process very similar to how seashells are formed. You take CO2 and react it with a metal, and it can form a mineral. In nature that mineral is predominantly calcium carbonate, or limestone. We take a lot of inspiration from these processes and we ask ourselves, what can we make that has similar properties to materials that we already use in construction? This is the whole premise of our lab: to use biology along with traditional material science to make biomimetic, responsive, even living material technologies for the built environment.
What is the potential for these materials to absorb carbon?
Yasemin: It’s fundamental. Eleven percent of the global emissions come from the materials we use, so there is an opportunity to change this. Until not long ago, the standard in our industry was to consider building emissions in terms of yearly performance. Even our policies looked at emissions and energy use yearly. We need a total shift — we need to look at the whole-life carbon cycle of a building, just like in nature. We don’t look at the impact and health of a forest in one year; we look at this over its entire lifespan. So for the built environment, we also need to embrace a whole life-cycle way of thinking. When we adopt this mindset, a new generation of carbon-sequestering materials will help us absorb carbon over the lifespan of a building. In essence, buildings can act more like a forest and clean the air that surrounds them.
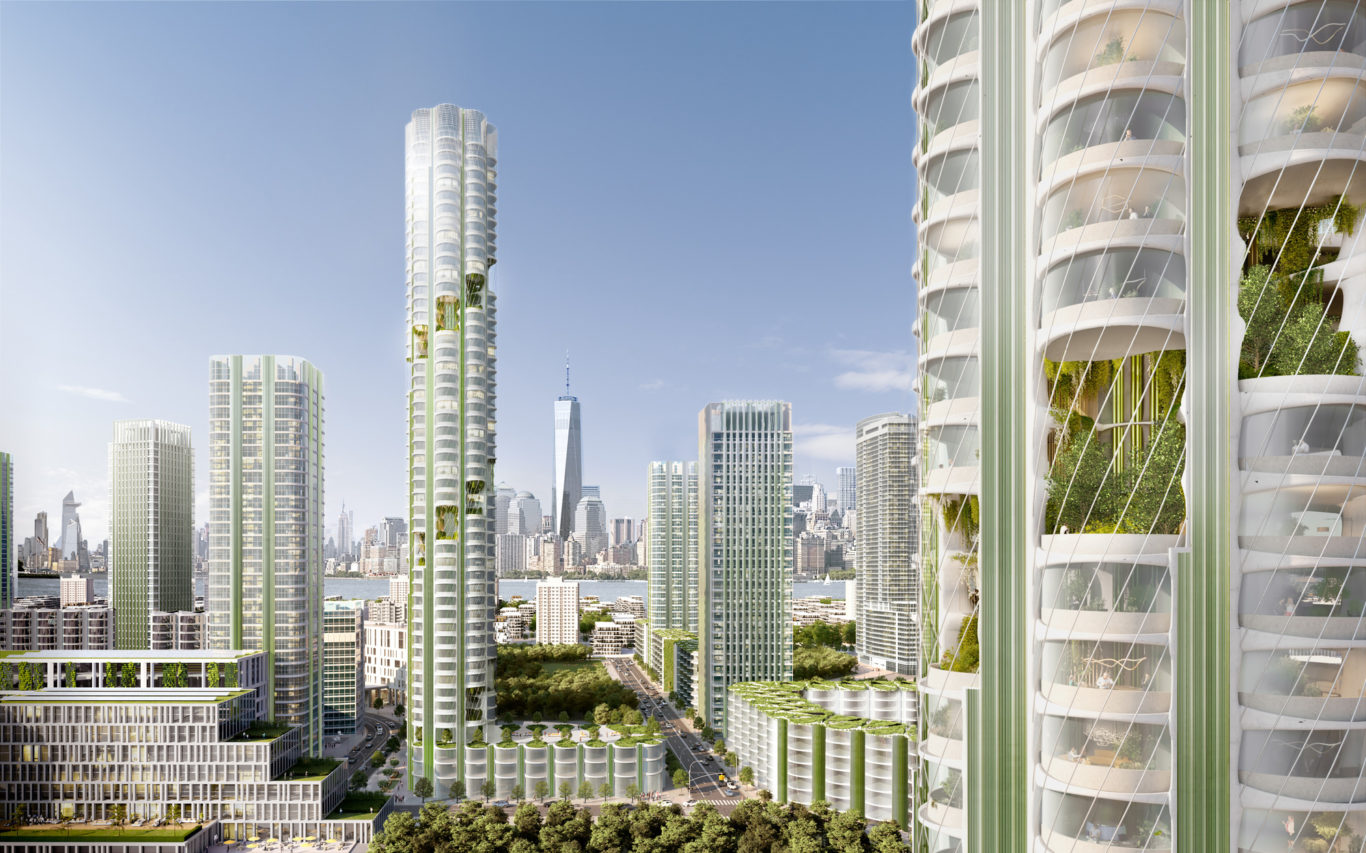
Wil: A lot of my inspiration comes from where I grew up, on a cotton farm and cattle ranch. I was surrounded by nature. When I moved to larger cities, I realized that I was the generation of my family that urbanized. When I go back home for the holidays, I go back to the farm.
For years I’ve asked myself, why is the built environment so sterile and static and non-living? The best image that evokes this is Central Park in New York City. When you look at the park from above, you see this sharp line between what is human-made and what is natural. But what if we could blur the boundaries? Could we go so far as to say that we can engineer life into our buildings? In fact, a building is a lot like the human body. It has a skeleton, the structure. It has a skin that regulates temperature and humidity. It’s a wired neural system. It consumes energy and produces waste.
The work that’s coming out of my lab is the very first step toward bringing building materials to life. And then we can start thinking about how to engineer buildings to continue to sequester carbon throughout their lifespan. Yasemin and I talk about this every time we meet. And that’s what’s behind the concept of Urban Sequoia. Why can’t buildings be like trees in a forest? Can they be mechanisms for carbon uptake, storage, and utilization? These little breakthroughs are getting us closer and closer to that reality.
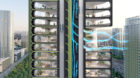
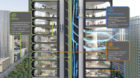
What does biological concrete look and feel like? How is it different from the concrete that we’re familiar with?
Wil: The research we’ve been doing here spans a wide range. Some of these materials are more plug-and-play, like alternative cements, alkali-activated cements, and geopolymer cements that have low embodied carbon. We also work a lot with cellulosic materials. We’re doing some work with bacterial cellulose — which is what you get in the process of making kombucha, for instance. This is a carbon-storing material that grows really quickly, faster than trees, faster even than some grasses. We engineer that to produce materials that look and feel like traditional materials and have similar properties.
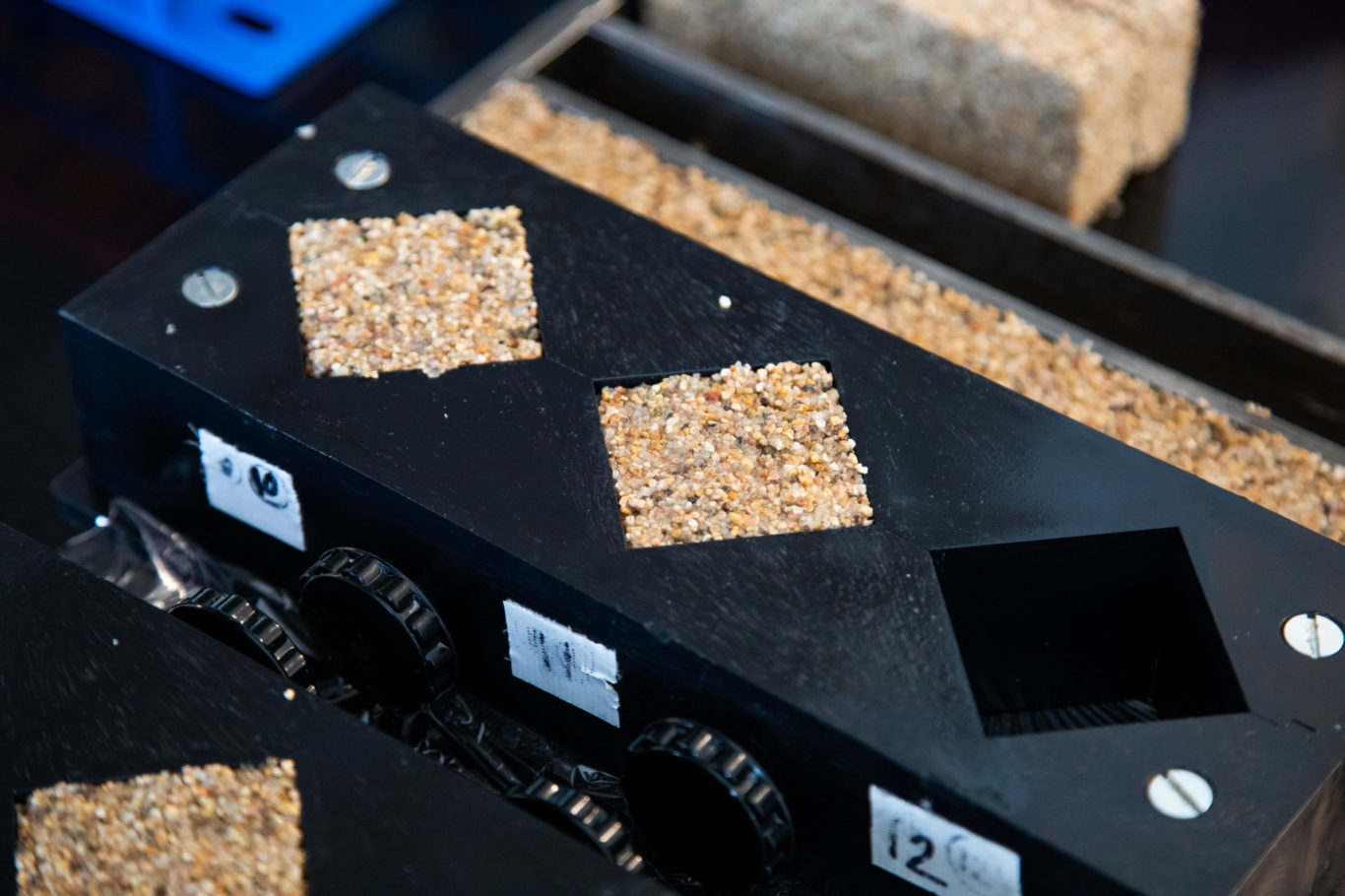
For the engineered living building material project, it was not important for us to have a product that looks exactly like portland cement concrete, or even behaves like it. We made something that is bioinspired and biologically produced. Because it is “grown,” it has its own unique properties and its own advantages. We’ve been very focused on making sure that we could meet the performance standards that would allow engineers and architects to specify our products — that really is the way that you enter the market — but the unique performance characteristics are what make it really exciting for architects and engineers.
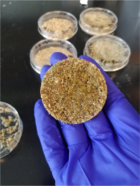
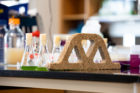
Biological concrete can have a very different aesthetic and tactile experience, depending on what kind of aggregate you use. Unlike traditional concrete, you can change the color and the texture. Like concrete, it can be molded in any shape. And we’ve found that it has compressive strength properties that are approaching that of traditional concrete, while its tensile properties and fracture resistance are radically different. This enables us to make brand new shapes and different morphologies that we haven’t been able to produce before.
We’re seeing such an interest in clean materials, and people are very eager to do good with that momentum.
Yasemin: This is very exciting for us as designers. It pushes us to think differently. We know how to design with concrete. We know how to design with timber. But now we’re working with a type of new material which has its own strengths and unique qualities. For example, perhaps we can design a structure that has less volume and more surface, to enable it to breathe more. This could lead to a whole new generation of buildings that adopt entirely new design strategies.
Wil: This speaks to why I’m so excited about our partnership. We’re a team of scientists and engineers; we think it’s really cool to be able to produce something and measure its properties. But the vision of how it can be applied in buildings, what new opportunities it can unlock — we’re a little short-sighted there. SOM is helping to bring that vision more into focus for us. They are showing us the design possibilities, and it’s kind of a perpetual motion machine — because every time I meet with SOM, I’m energized to go back to the lab and to try to create something even more incredible.
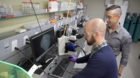
Yasemin: That’s exactly how things advance, right? When scientists and creatives come together, amazing things can happen. This is potentially one of those moments.
What are the challenges ahead in getting to the point where these solutions can be widely adopted?
Yasemin: Just like any new material or developing technology, it will require investment and applications. It requires education and sharing knowledge as well. It’s a great opportunity and all of the dials are moving in the right direction: we’re seeing an increase in investment; we’re seeing an increase in interest; we’re seeing an increase in policies and incentives, as well as individuals and professionals like us who are interested to make this happen and are working to implement it as quickly as possible.
Wil: We’re living in a really exciting time. There is beginning to be a pull from the AEC industry for new materials and other building technologies that address the global climate crisis. There’s a massive momentum in building, and we know that this will continue. When you think about construction on a global scale, that could be a mechanism to heal the planet, or further harm it. I think we’re seeing such an interest in clean materials, and people are very eager to do good with that momentum.
This is a huge wave and we’re just at the beginning. We’re going to see so much more in terms of new materials, new technologies, new policies, new ways of designing, building, and thinking.
Along with this come the challenges. Construction is definitely a commodity industry. Economics typically reign supreme. We always have to be cognizant of cost. We have to be aware of perception as well, so talking about living materials, a global pandemic was probably not the best time to launch a new biological material and suggest that we put it in our buildings, even though our algae-based concrete is completely non-toxic and harmless — it’s basically akin to having a plant inside of your building blocks. Despite minor perception challenges, we are seeing a lot of champions for clean material technologies — and for the solutions that we’ve been developing, we’re seeing much lower barriers in terms of perception because we’re demonstrating performance and economic viability. This isn’t just some ivory-tower idea. We are transitioning this into the commercial space, and we have incredible partners to help us do that.
So, when are we likely to see the first living concrete building?
Wil: It may happen sooner than you think. We’ve founded a company, Prometheus Materials, and we have licensed the IP to begin manufacturing these materials. And our teams — SOM, the University of Colorado, and Prometheus — have been collaborating on product design ideas and prototyping projects.
In the short term, it’s really important to manufacture a product that has the performance attributes to be able to meet the current building code, so we can enter the market. We want to ensure that architects, engineers, even building owners become familiar with it and they understand how to design with it.
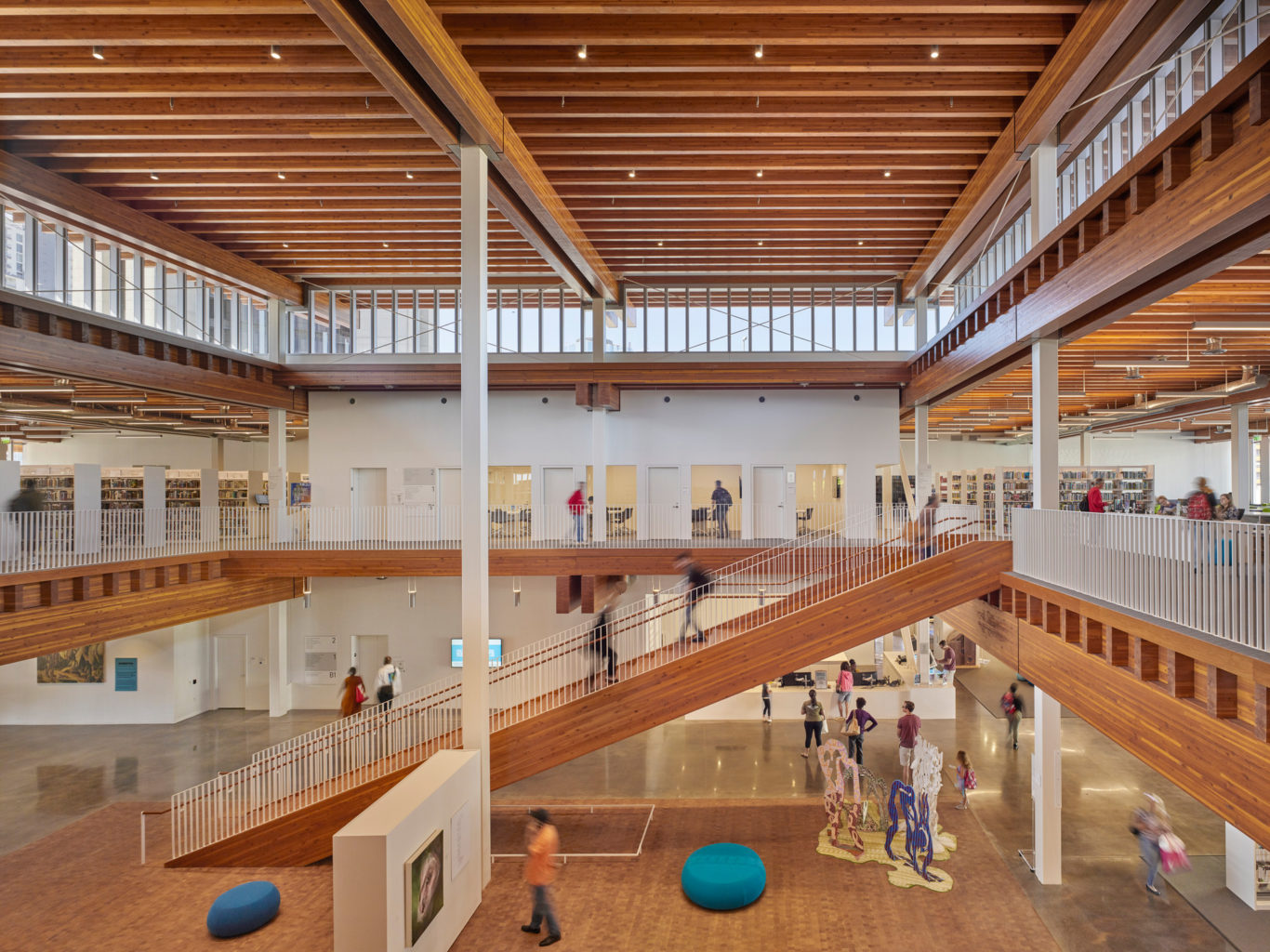
But just look at what’s happened with mass timber, and how quickly the building code has responded to allow for the increased use of timber — that’s a biological material, as well. Yes, the design tools needed to be engineered and the code needed to be revised, but we’ve seen that happen at unprecedented speeds. That has paved the way for other new material technologies.
Yasemin: We’re also seeing legislation that is actively pushing for the use of low-carbon materials, and eventually toward carbon-sequestering materials. As we see more and more of this all over the world, I’m not sure that these things are going to be optional.
Wil: I really expect that in the next 5 to 10 years we’re also going to see tremendous innovations in the realm of carbon storage and carbon negativity — and together with that, a change in the design philosophy that architects and engineers use to design buildings. So if we’re really striving toward absolute zero carbon — and by absolute zero, I mean zero embodied and operational carbon, or, better yet, it’s net carbon-negative, and we transform buildings into net carbon sinks — we have to understand and use these emerging carbon-storing materials in sufficient quantities to counteract the carbon-emitting materials. So, be on the lookout for a lot of additional innovations related to building materials and carbon storage.
Yasemin: This is a huge wave and we’re just at the beginning. We’re going to see so much more in terms of new materials, new technologies, new policies, new ways of designing, building, and thinking. We are living a historic shift in real time. And our collaborations and collective efforts are helping to shape that future.